BACKGROUND OF THE PROJECT
With the increase in vehicle scrapping and indoor air conditioning replacement, a large number of discarded copper and aluminum radiators are produced. Since discarded radiators contain a large amount of valuable non-ferrous metals, the number of customers who specialize in the recycling of air conditioning radiators is also increasing. However, with the rapid development of the economy, labor costs have increased significantly. The traditional recycling method of air conditioning radiators is no longer applicable, and has been replaced by advanced air conditioning radiator crushing and separator equipment.
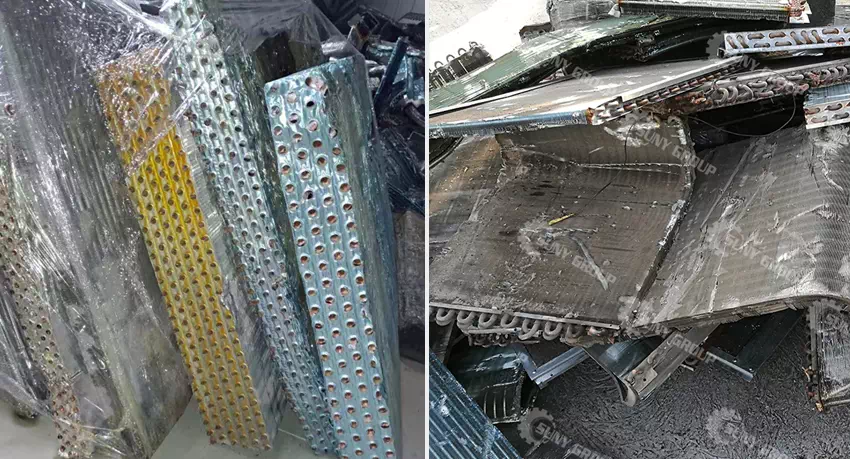
WORK VIDEO
WORKING PRINCIPLE
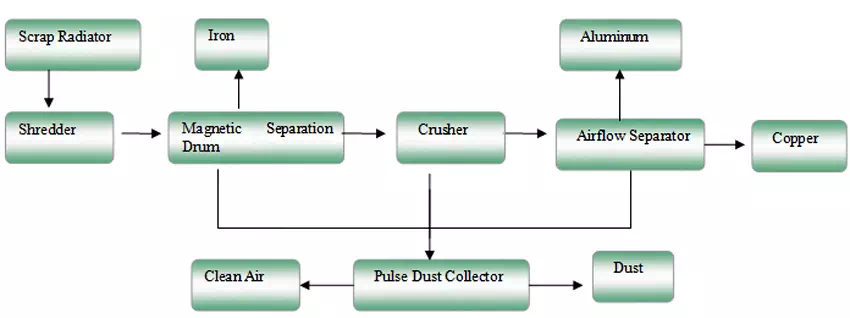
The copper and aluminum radiator separator adopts mechanical crushing processing. It is a batch processing equipment. First, the air conditioning radiator is transported to the crusher for processing through the feeding conveyor. Subsequently, copper and aluminum are completely separated by sorting equipment using the principle of different specific gravity. In this way, the output of the entire production line is relatively high.
The scrap copper and aluminum radiator recycling production line adopts the method of physical crushing, sorting and recycling. First, the materials are coarsely crushed by the primary crusher, and then crushed by the secondary crusher to crush them into materials of about 3 cm in size. Subsequently, iron impurities are removed through magnetic separation, and then air separation is performed. The result is pure iron, copper and aluminum that can be recycled and reused.
KEY EQUIPMENT
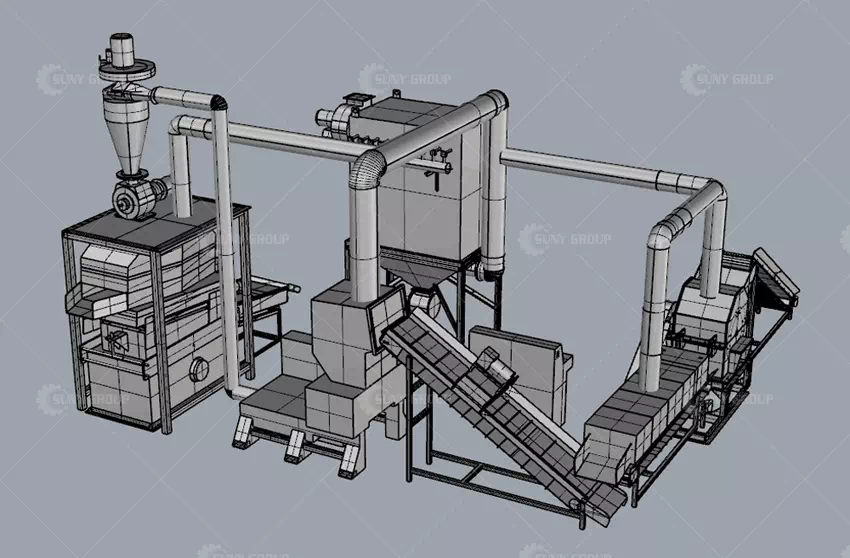
1. Conveying equipment:
Conveying radiators, shredded radiators, crushed radiators, and sorted radiators
2. Crushing system
Level one shredding: shredding radiators from large to small sizes
Secondary crushing: crushing small size to particles
3.Magnetic separation system
Strong magnetic sorting equipment: remove iron from copper and aluminum
4. Air flow sorting system
Air flow sorting equipment: Separating copper and aluminum through air flow
5. Pulse dust removal system
Pulse dust removal equipment: collects dust in the crushing and screening stages of the production line and crushed aluminum chips powder
EQUIPMENT ADVANTAGES
1. This production line has been developed by our company for many years. Compared with the processing technology in European and American countries, our processing process has lower metal loss, minimizes the number of times the material is broken, and ensures that the material is separated in a large state, thereby reducing metal loss. The generation of powder improves recycling efficiency.
2. The first crusher adopts a two-axis roller design, which has low noise and high torque, and can crush larger radiators.
3. The cutting tools of the secondary crusher are made of alloy tool steel, which are processed by special processes and have a longer service life.
4. Using two-pole specific gravity sorting, the sorting accuracy is improved, and the purity of the sorted copper, aluminum, and iron is >99%.
5. The treatment process is closed and equipped with a dust collection system to effectively control dust overflow.
TECHNICAL PARAMETERS
Model Capacity(Kg/H) Sorting Efficiency Dust Removing Efficienty Power(Kw) HNRP-1000 1000 97% 99% 55*2 HNRP-2000 2000 97% 99% 75*2 HNRP-3000 3000 97% 99% 115*2 HNRP-5000 5000 97% 99% 145*2
CUSTOMER SITE

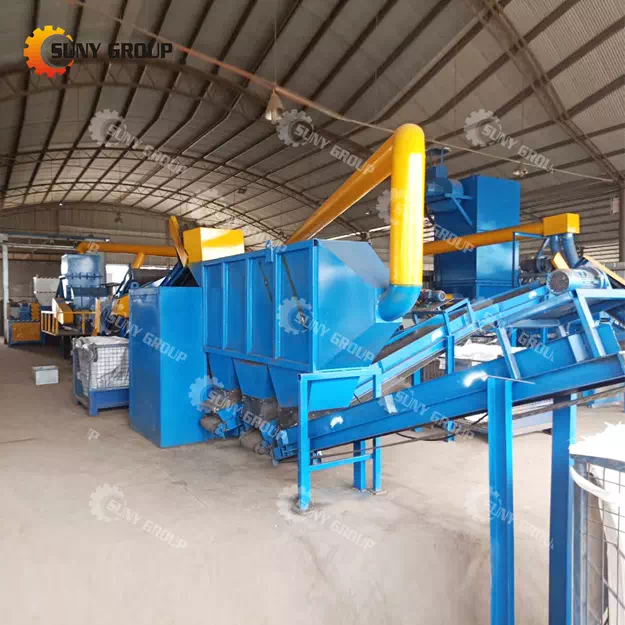