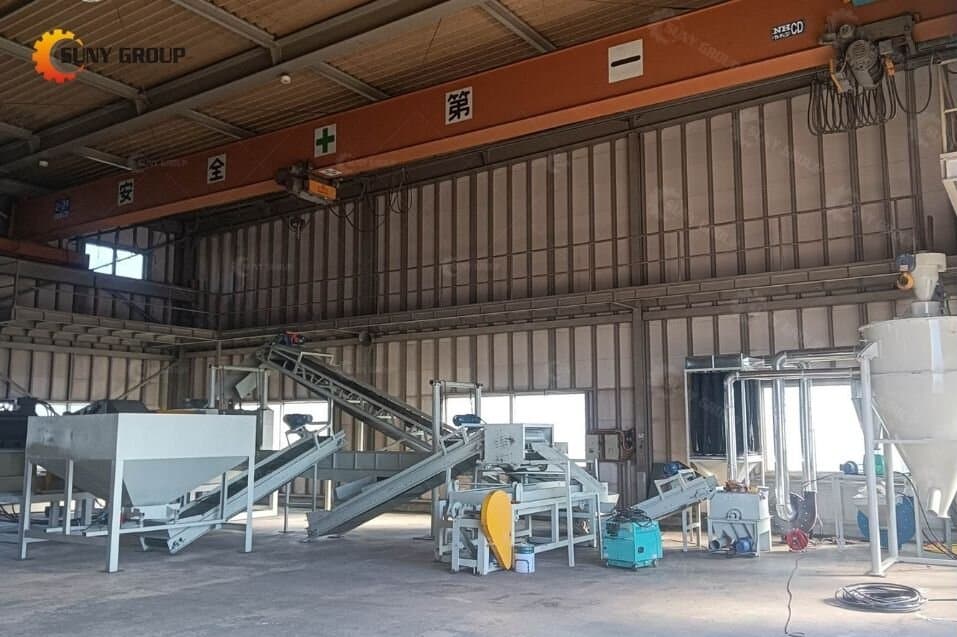
Author: zzsuny
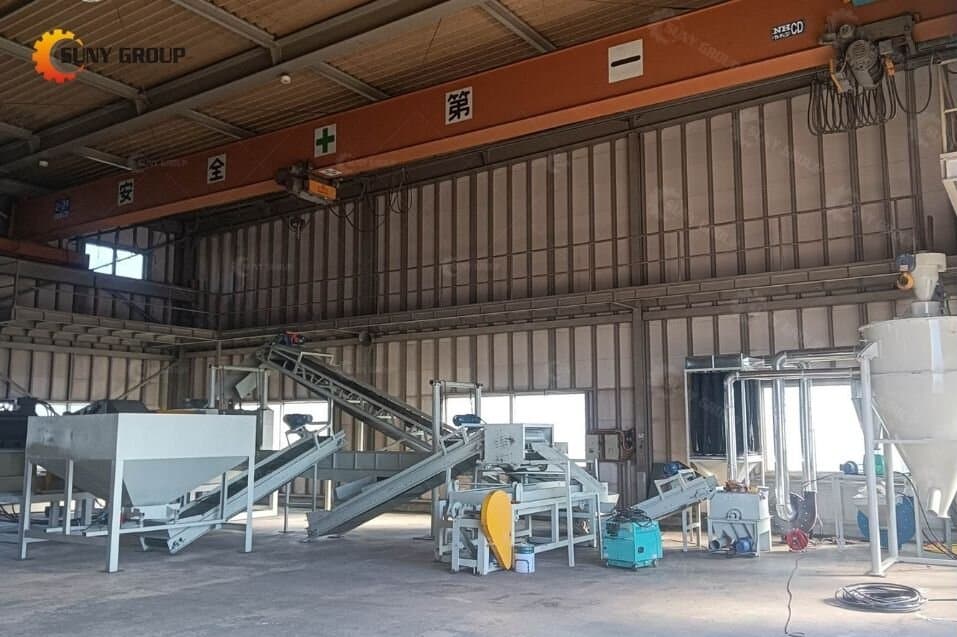
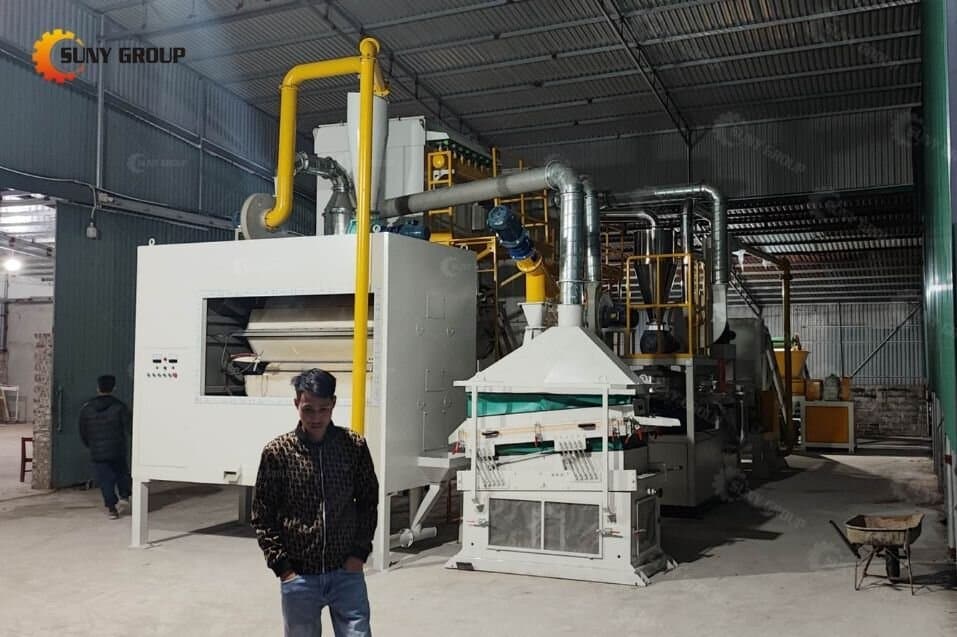
Vietnam customer circuit board crushing recycling line work site
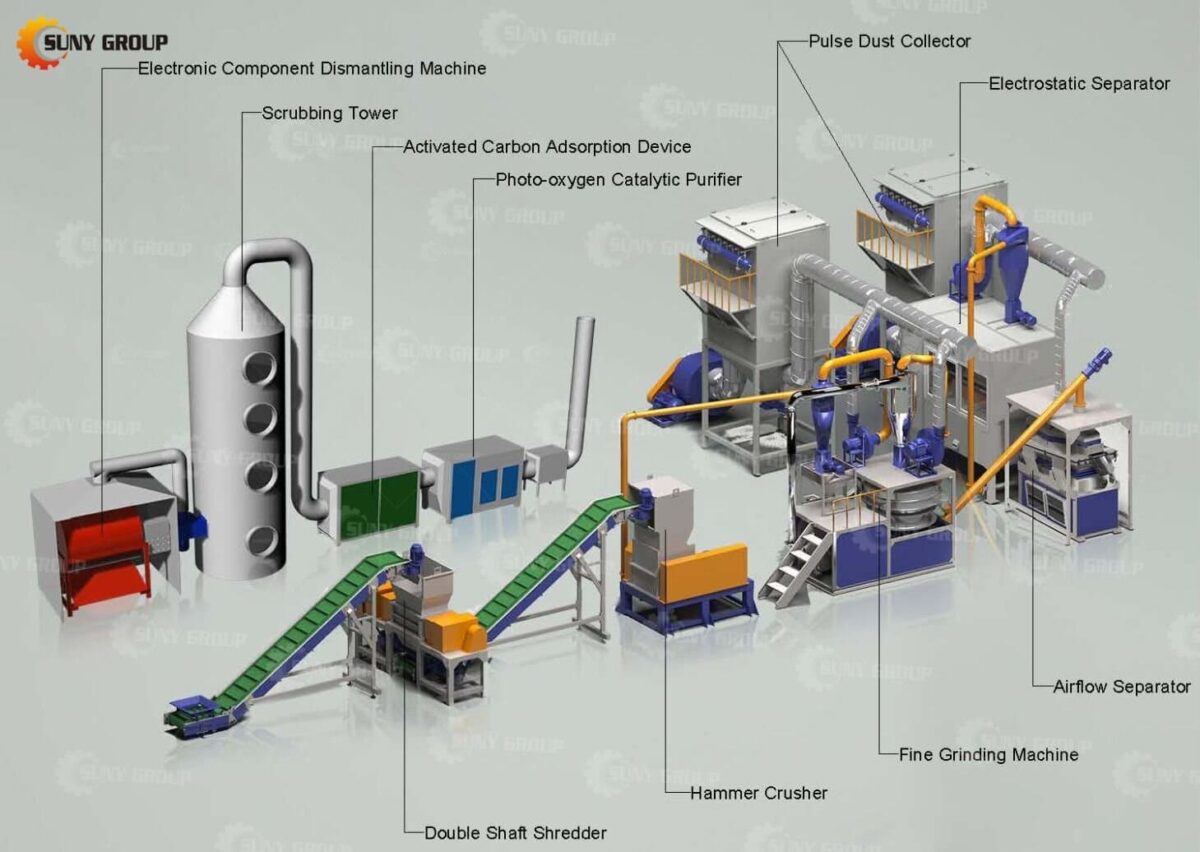
Here’s a closer look at the key machines included in modern e-waste recycling management systems:
1.Shredders and Crushers
Shredders and crushers are the first step in the e-waste recycling process. These machines break down large electronic devices, such as computers, televisions, and appliances, into smaller, manageable pieces. This step prepares the materials for further processing and ensures efficient separation of components.
2.Electrostatic Separators
Electrostatic separators are used to separate mixed materials, such as plastics and metals, based on their electrical conductivity. This machine is particularly effective for recovering precious metals like gold, silver, and palladium from circuit boards and other electronic components.
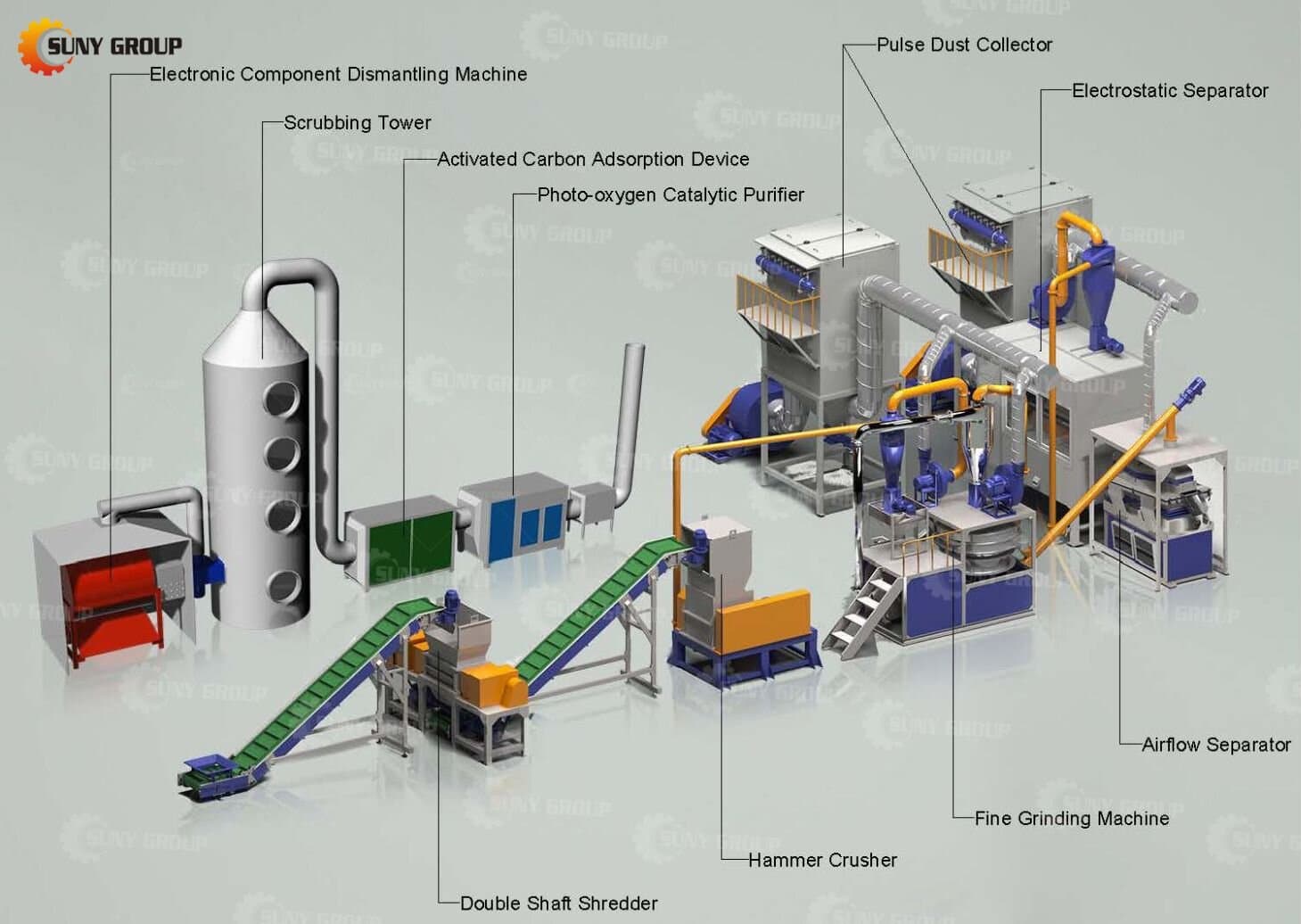
E-Waste Recycling Management Equipment
3.PCB Component Dismantling Machine
The Efficient PCB Component Dismantling Machine is a state-of-the-art solution designed to safely and effectively remove electronic components from printed circuit boards (PCBs). This machine uses advanced heating and precision tools to detach components without damaging the PCB or the parts, ensuring maximum recovery of valuable materials. It is a critical step in the recycling process, as it allows for the reuse of functional components and the extraction of precious metals.
4.PCB (Printed Circuit Board) Recycling Machines
Specialized PCB recycling machines are designed to process and recover valuable metals from printed circuit boards, which are a significant component of e-waste. These machines use a combination of crushing, grinding, and separation technologies to extract metals like copper, gold, and silver.
For more information on e-waste recycling solutions and equipment, visit our Website or contact us.
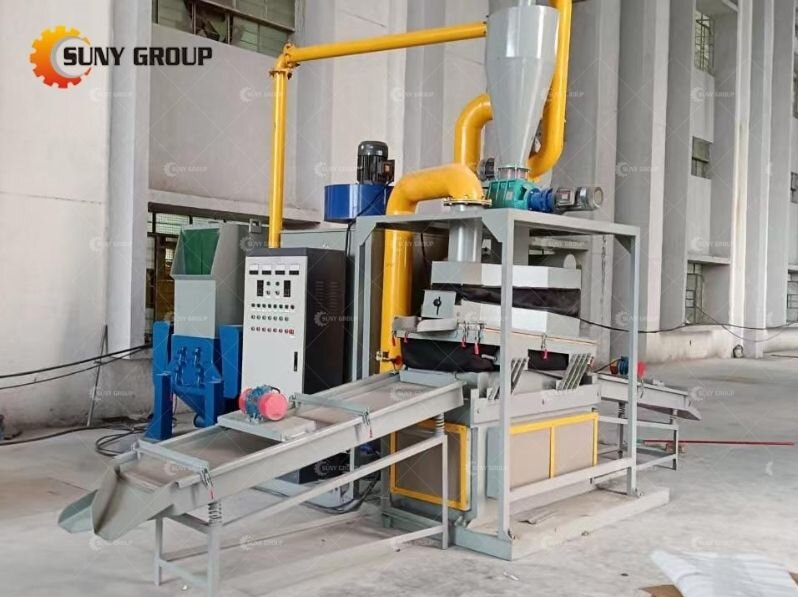
India customer cable granulator machine workshop
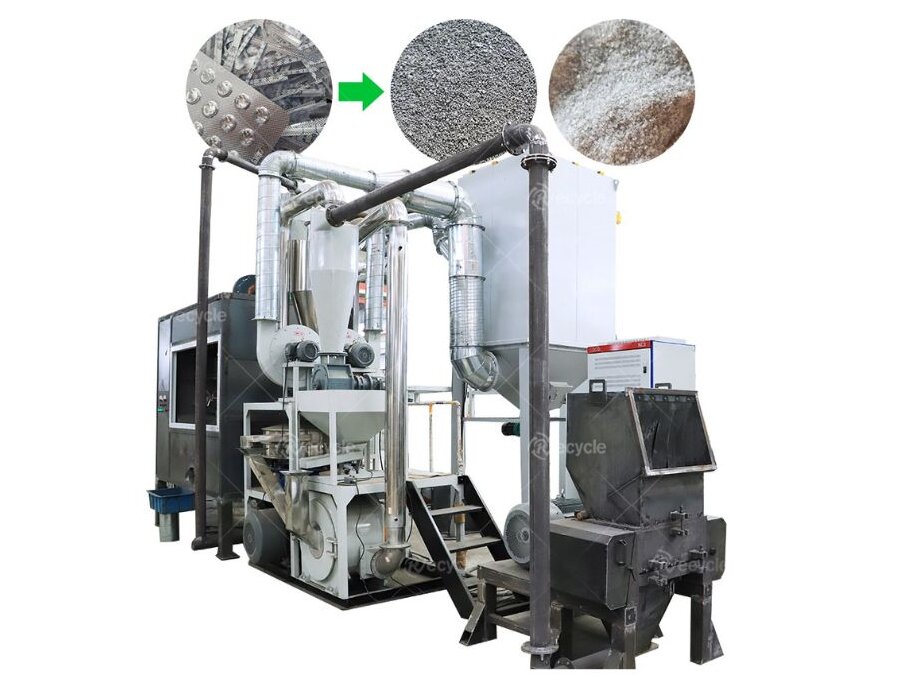
The Challenge of Medical Blister Waste
Medical blister packs, commonly used for packaging tablets and capsules, are composed of aluminium and plastic composites. While these materials ensure the safety and efficacy of medications, they pose a significant environmental challenge at the end of their lifecycle. Traditional disposal methods, such as incineration or landfill, contribute to pollution and resource wastage. According to industry estimates, billions of blister packs are discarded annually, creating an urgent need for sustainable recycling solutions.
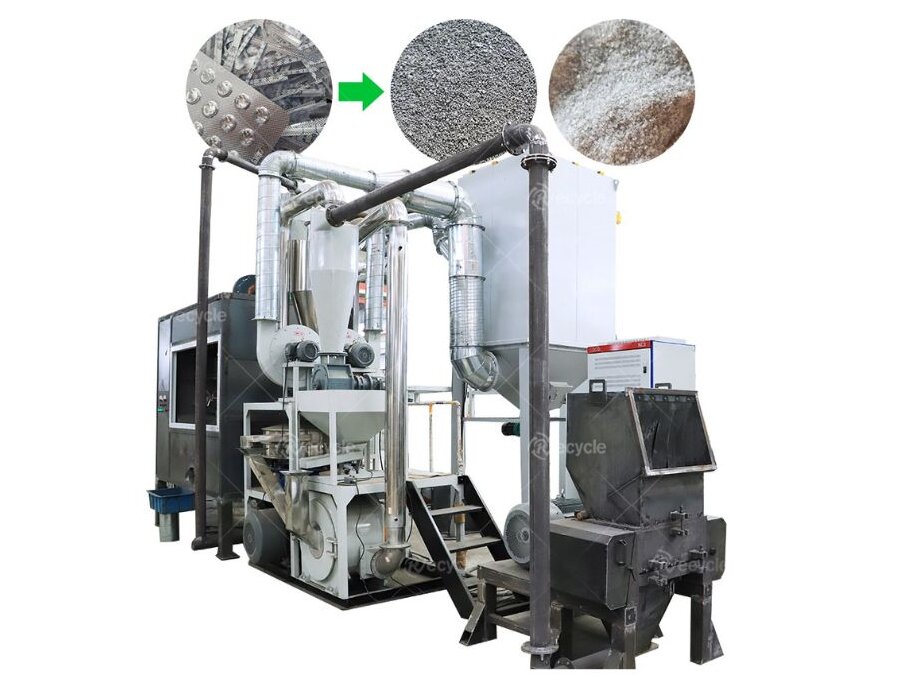
Aluminium Blister Recycling Machine for pharmaceutical waste disposal
How the Aluminium Blister Recycling Machine Works
The Aluminium Blister Recycling Machine employs a sophisticated, multi-step process to recover valuable materials from waste blister packs:
Crushing: The blister packs are shredded into small pieces, typically around 10mm in size.
Grinding: The pieces are further pulverized into fine powders using a water-cooled grinding system to prevent overheating.
Separation: An electrostatic separator is used to isolate aluminium from plastic, achieving a purity rate of over 99%.
Dust Control: Advanced pulse dust collectors ensure a clean and safe working environment, minimizing environmental contamination.
This fully automated process, controlled by a PLC system, requires minimal human intervention and can process up to 800 kg of waste per hour, depending on the model.
Global Adoption and Future Prospects
The demand for aluminium blister recycling machines is growing worldwide. For instance, a high-capacity machine was recently installed in Algeria, where it successfully processes medical blister waste with a separation rate exceeding 99%. For more information on how to integrate this technology into your operations, contact leading manufacturers like us today.
E-Waste and PCB Recycling Machinery
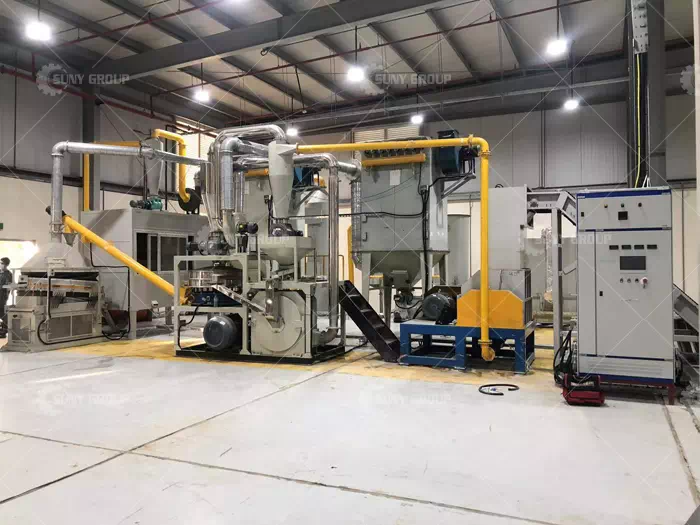
With the rapid development of science and technology, the replacement of electronic products has become faster and faster, resulting in a large amount of electronic waste (E-Waste) generated. Printed Circuit Board (PCB) is the most common type of E-Waste, which contains valuable metals such as gold, silver, copper, etc. Recycling these materials can effectively reduce the waste of resources and protect the environment.
Recycling of e-waste needs to be accomplished through a series of specialized equipment. The recycling process is usually divided into several steps, mainly relying on crushing and sorting equipment, physical separation equipment, and chemical recycling equipment.
Circuit Board Recycling Equipment in Qatar
First, the crushing and sorting equipment crushes the e-waste to reduce the volume of the material and prepare for the subsequent separation work. Next, physical separation equipment, such as magnetic separation, electrostatic separation, and eddy current separation, separates metallic and non-metallic materials in the waste through different physical principles, respectively. Finally, chemical recycling equipment extracts valuable metal components such as gold, silver, and copper from waste PCBs through methods such as hydrometallurgy or solvent extraction.
The application of e-waste and PCB recycling machinery offers significant advantages. Firstly, these machines are able to dramatically increase recycling efficiency, which is much faster and more precise than manual processing. Second, through efficient physical and chemical separation, they can maximize the recovery of valuable resources in e-waste and reduce resource waste.
With the increasing volume of e-waste, the role of recycling machinery has become particularly important. Effective recycling can not only reduce the accumulation of waste but also extract valuable resources and create economic benefits for enterprises. At the same time, it reduces the emission of harmful substances, helps protect the environment, and promotes sustainable development. If you are interested in an e-waste recycling machine or have the need, please feel free to contact us for consultation.
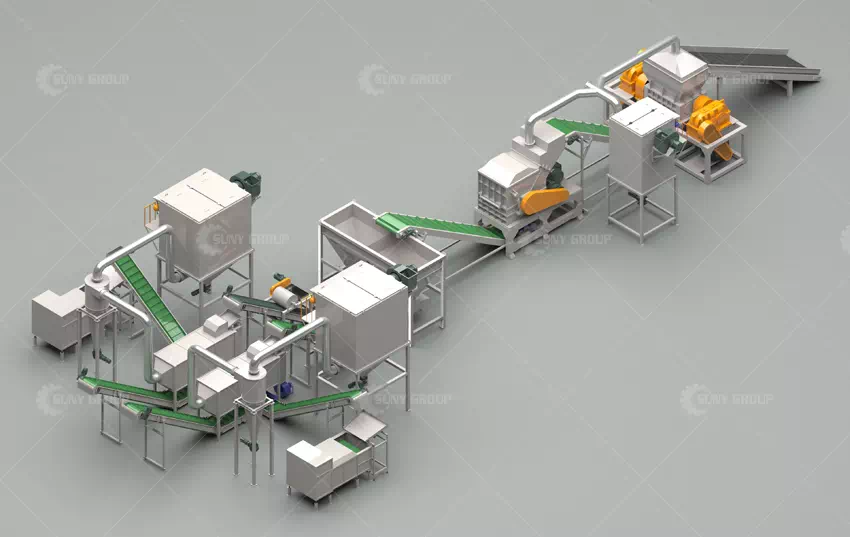
Radiators, as important heat dissipation components, contain many metals and other valuable materials inside. How to effectively recycle these used radiators and extract useful resources from them is a key challenge in the environmental protection and resource recycling industry, and the Radiator Crushing and Sorting Recycling Machine developed by SUNY GROUP is precisely designed to solve this problem. It can quickly and accurately complete the radiator crushing and sorting. It can quickly and accurately complete radiator crushing and sorting, contributing to environmental protection and resource recycling.
Radiator Crushing and Sorting Recycling Machine
Working Principle of Crushing and Sorting Recycling Machine
The first step in the radiator recycling process is crushing, in which waste radiators are physically crushed by the crusher. The crusher utilizes a powerful cutting force to break the radiators into small pieces or granules, which facilitates the subsequent sorting process. The crushed material usually includes aluminum, copper, iron, and other metallic and non-metallic substances. Through an efficient crushing process, recycling efficiency is maximized and the integrity of each material is ensured.
The next step is sorting, where the crushed material is separated through a series of sorting equipment. Common sorting methods include airflow sorting, electromagnetic sorting, and electrostatic sorting, which effectively separate different metals, plastics, and rubbers to ensure that each material is accurately recycled. In this way, different types of metallic materials can be recycled separately, while non-metallic materials can be processed or reused in other ways.
>Machine components and technical specifications
The main components of the machine include a crusher, sorting equipment, a conveying system, and a control system. The crusher ensures high crushing capacity by breaking up the radiators with its high-strength blades and power system. The sorting system includes a variety of sorting equipment, such as airflow sorters and electromagnetic separators, to ensure the accurate separation of different materials.
The technical specifications of the machine include a highly efficient production capacity capable of processing large quantities of used radiators in a short period. The machines are usually designed for durability and stability over long periods of operation and are able to adapt to high-intensity production environments. In addition, the machine’s control system is usually equipped with an intelligent operator interface for easy operation and real-time monitoring of the machine’s operating status to ensure continuous and efficient production.
Applications
The machine is widely used in the recycling of all kinds of used radiators. Whether in the automotive industry or home appliance industry, the recycling of waste radiators is of great significance. In the automotive industry, car radiators are an important source of metal resources, especially aluminum and copper, which can be used to produce car parts or other industrial products. In the home appliance industry, radiators in air conditioners, refrigerators, and other equipment also contain a large amount of valuable metal materials, and these radiators can provide valuable raw materials for the manufacturing industry through recycling.
In addition, the equipment can also be used to process radiators in industrial equipment, such as those in large mechanical equipment and generator sets. These radiators can be crushed and sorted to recover a large amount of metal material for secondary production.
Radiator Crushing and Sorting Recycling Machines play a vital role in the recycling and reuse of waste radiators. Through advanced crushing and sorting technology, this machine not only effectively extracts valuable metal materials, but also reduces the environmental impact of waste and contributes to the recycling of resources. If you have the need welcome to contact us for more information and price.
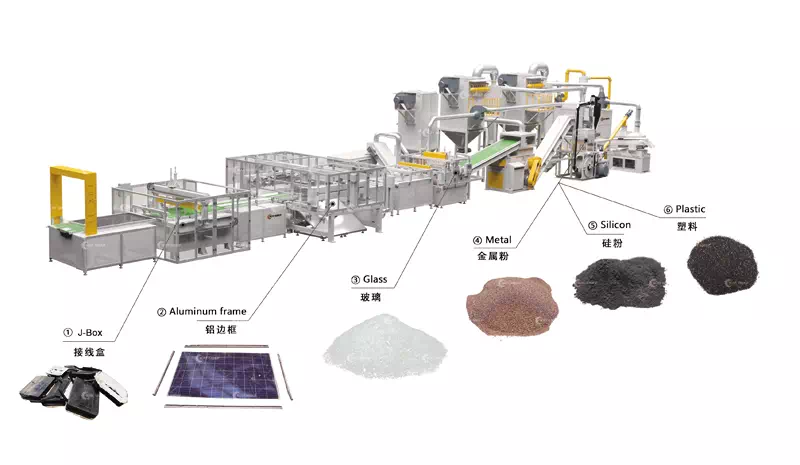
Solar energy and photovoltaic panels, as an important component of renewable energy, are being used more and more widely for energy production worldwide. However, with the rapid development of the photovoltaic industry, the number of end-of-life solar and photovoltaic panels is increasing every year. If not properly disposed of, these end-of-life panels may pollute the environment. Therefore, the emergence of solar and PV panel recycling machines has become an important tool to solve this problem.
SUNY GROUP has developed PV Panel Recycling Machines to efficiently process used solar and PV panels through advanced technology and automated systems. These machines can decompose and recycle glass, metal, battery cells, and other valuable materials from the panels, thus realizing the reuse of resources, reducing environmental pollution, and supporting the development of a circular economy.
Solar & Photovoltaic panels recycling Machine
In terms of design and functionality, PV panel recycling machines embody a high degree of technological integration and environmental protection. The structure and components of the machine are the basis for its efficient operation. Generally speaking, such machines consist of a crushing device, a separation system, a recycling module, and an intelligent control system. The crushing device breaks down the PV panels into smaller components for subsequent separation and recycling. The separation system utilizes physical or chemical methods to separate different materials in the panels such as glass, silicon wafers, and metals, while the recycling module is responsible for further processing these materials to reusable standards.
Automation features are a highlight of the PV panel recycling machine. By integrating intelligent sensors and control software, the machine can automatically recognize, sort, and process different types of panels. This not only improves processing efficiency but also reduces the need for manual labor and significantly lowers operating costs. In addition, these machines are often equipped with real-time monitoring and data analysis features that allow operators to keep track of the equipment’s operating status, thereby optimizing the production process.
Safety and environmental features are also key design considerations for PV panel recycling machines. To ensure safe operation, machines are often equipped with multiple safeguards, such as overload protection, emergency shutdown functions, and seals to prevent leakage of hazardous substances. In terms of environmental protection, these machines use non-polluting or low-polluting processes to minimize their impact on the environment. For example, during the process, the machine will effectively treat the waste gas and liquid generated to ensure compliance with environmental standards.
The importance of PV panel recycling machines is not only reflected in their contribution to environmental protection but also their economic and social impact. By recycling and reusing materials from PV panels, these machines can reduce the need to produce new materials, thereby reducing the waste of resources. At the same time, the rise of the PV panel recycling industry creates a large number of employment opportunities for society and promotes the development of green industries.
Pet Bottles Shredding Machine
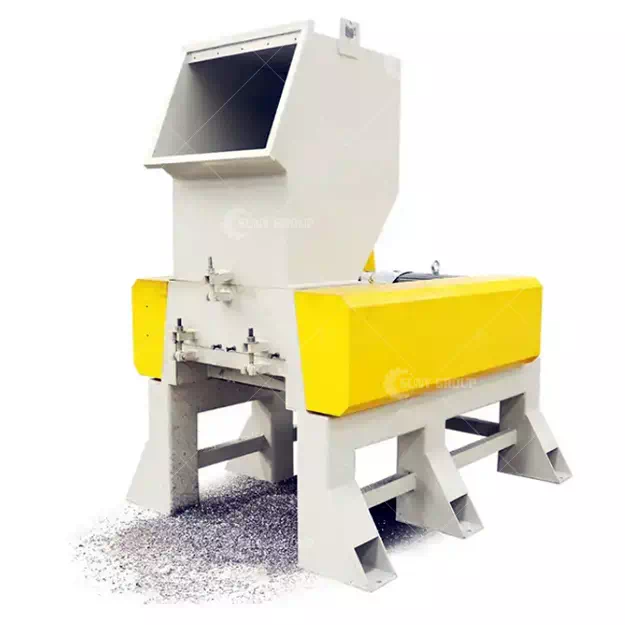
PET bottles (polyethylene terephthalate bottles) are widely used in the beverage, cosmetic, and pharmaceutical industries because they are lightweight, durable, and recyclable. However, with the increase in consumer packaging, the number of PET bottles being discarded has risen sharply. How to efficiently recycle and reuse these discarded PET bottles has become an important challenge for the current waste recycling industry.
The PET bottle crusher developed by SUNY GROUP, as a specialized equipment for processing PET bottles, has become one of the key equipment in the plastics recycling industry due to its highly efficient crushing capacity and easy operation.
PET bottle crusher usually adopts a high-speed blade rotating cutting method to crush PET bottles into small flakes or small particles through the cutting action of multiple blades. The blades inside the equipment can adjust the cutting size according to different needs, thus obtaining different sizes of fragments. These flakes can be further processed in the subsequent recycling process or made into new PET products by hot melting and chemical treatment.
Firstly, the waste PET bottles are fed into the crusher via a conveyor belt. The cutting system of the crusher quickly cuts the PET bottles into small flakes or pellets. Because PET bottles are relatively soft and tough, the crusher usually needs to be designed with an efficient and durable blade system to ensure intense crushing in a short period. The crushed PET flakes can be further screened, cleaned, and processed for recycling purposes.
The control system of the PET bottle crusher plays a vital role in the operation process. Through automated control, the operator can set the crusher according to different needs and adjust the crushing precision, speed and blade wear. This allows the PET bottle crusher to meet the demands of mass production while maintaining a low failure rate and long service life.
Advantages of PET bottle crusher.
PET bottle crushers can process waste PET bottles efficiently and greatly improve recycling efficiency. With the increasing global demand for plastic recycling, PET bottle recycling has become particularly important. The use of a crusher can quickly break down PET bottles into small reusable pellets, greatly increasing productivity and reducing the time and cost of manual processing.
PET bottle crushers are often designed with a focus on the user’s operating experience, featuring an easy-to-use interface and an easy-to-maintain structure. Operators can easily make settings and adjustments to the equipment to ensure that the machine is always in the best working condition. Moreover, the maintenance of the equipment is also very simple, and the replacement and cleaning of the blade system can be completed through standardized processes, which greatly improves the service life and production stability of the equipment.
PET bottle crusher is suitable for all types of waste PET bottles, whether it is mineral water bottles, carbonated beverage bottles, or other types of plastic bottles, can be processed efficiently. In addition, the crusher can also be applied to all kinds of plastic recycling industry, not only limited to PET bottles but also can deal with other plastic waste, with strong adaptability.
PET bottle crusher, as the core equipment for waste PET bottle recycling, can effectively improve recycling efficiency, reduce the waste of resources, and reduce environmental pollution through efficient crushing and separation technology. With the rapid development of the recycling industry and the increasingly strict environmental protection policy, PET bottle crushers will be more and more important in the future market. If you need or want to know more, please feel free to contact us for consultation.
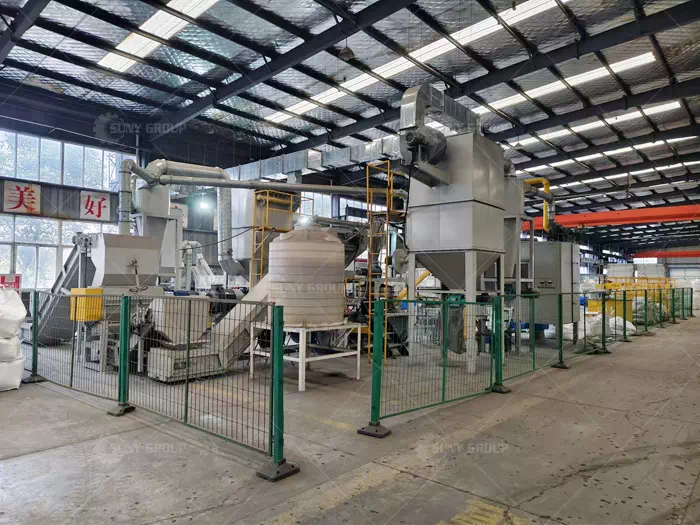
Solar PV Panel Recycling Equipment in Jiangsu
Lithium Battery Recycling Equipment in Korea
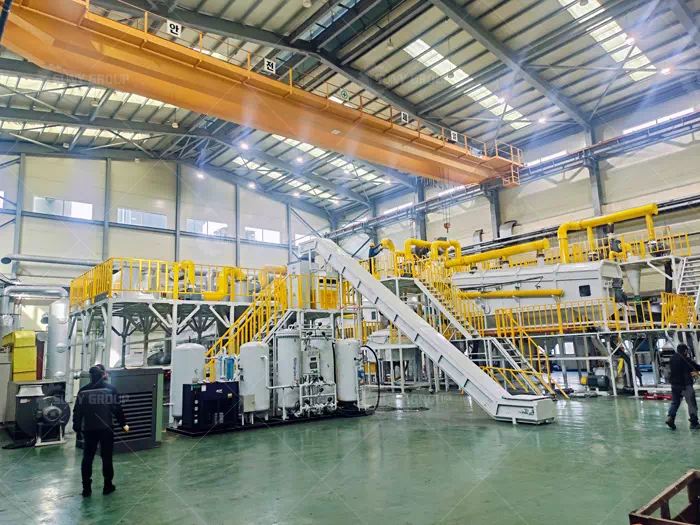
Scrap (WEEE) Shredders Machine for Recycling
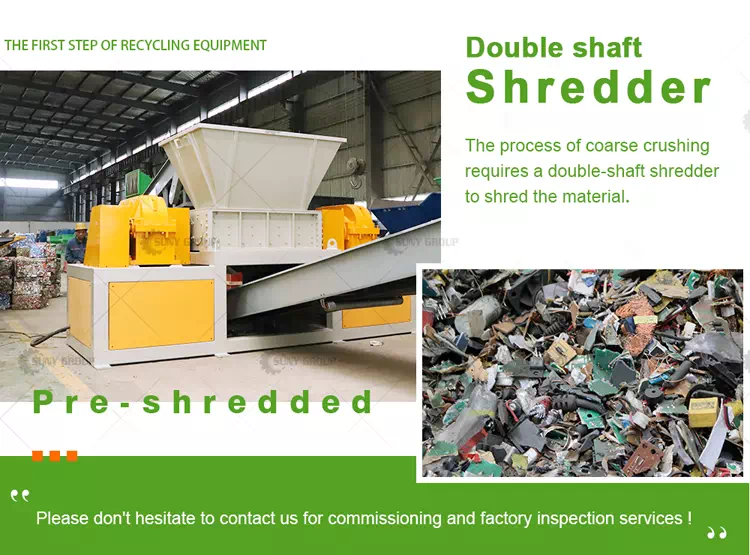
With the rapid replacement of electronic equipment, the treatment of Waste Electrical and Electronic Equipment (WEEE) has become one of the key tasks in global environmental protection. Waste shredders play a crucial role in the WEEE recycling process, which can effectively process waste electronic products such as circuit boards, hard discs, plastic casings, etc. preliminarily to reduce the volume and facilitate subsequent resource recovery and sorting. Through the efficient shredding of the shredder, companies are better able to extract valuable metals, plastics, and other resources to promote the recycling of e-waste.
Scrap (WEEE) Shredders Machine for Recycling
There are various types of waste shredders, the most common of which are dual-shaft shredders. Dual-axis shredders cut materials through two rotating knife shafts interlaced with each other, which is suitable for dealing with hard waste, and is widely used in the fields of electronic waste, used circuit boards, and metal recycling. Compared with single-shaft shredders, dual-shaft shredders have higher processing capacity and greater adaptability to cope with a wide range of waste materials quickly and effectively. In addition to this, modern waste shredders are constantly evolving in terms of automation and intelligence, equipped with intelligent sensors and control systems that can automatically adjust operating parameters to enhance operational precision and safety.
Waste shredders are widely used in WEEE recycling. Firstly, it can shred waste electronic equipment such as mobile phones, TVs, computer casings, hard discs, etc. to facilitate subsequent sorting and resource recovery. Especially when dealing with waste circuit boards, the waste shredder can shred them efficiently, from which precious metals such as gold, silver, and copper can be extracted, aiding metal recycling and reuse. In addition, waste shredders are also used to destroy storage media such as hard discs, ensuring complete data destruction and information security.
Waste shredders not only have high durability and efficiency, capable of working stably during long hours of high-load operation but also optimize the operation process through intelligent technology. Intelligent shredders can monitor the operating status of the equipment in real-time and automatically adjust the working parameters to improve the efficiency of the equipment and reduce the failure rate. For the WEEE recycling industry, the intelligence and efficiency of waste shredders are the key to increasing productivity and reducing environmental pollution.
The role of waste shredders in WEEE recycling cannot be ignored. They greatly improve the recycling efficiency of WEEE through efficient shredding and sorting, providing important support for resource reuse. With the development of technology, waste shredders will continue to play an important role in the environmental protection industry, promoting the treatment of electronic waste in a more efficient and environmentally friendly direction.